A lost art: Using brittle coatings to measure strain in complicated structures
- Harsh Bhundiya
- Jul 12, 2022
- 5 min read
Updated: Aug 7, 2022
Today the state-of-art method for strain measurement is to use expensive digital image correlation (DIC) systems which triangulate the deformation of your specimen during mechanical testing. But did you know that before this technology became mainstream, engineers relied on a simple yet effective technique for strain measurement, that of applying brittle coatings to specimens?
Mechanical testing is a vital part of engineering, as it provides a direct measurement of a component’s strength before any potential application. In many ways it is the ultimate test of our models. As Henri Poincaré put it: “Experiment is the sole source of truth. It alone can teach us something new; it alone can give us certainty.” This certainty is certainly of primary importance when building bridges, airplanes, and skyscrapers. Hence to verify the strength of our designs, engineers have devised ingenious ways of testing specimens from the nanometer scale (e.g. nano-indenters for architected materials) to the meter scale (e.g. loading jigs for static and fatigue testing of airplanes). And these setups are not haphazard; today engineers use the latest cameras, load cells, and electronics to measure both load and displacement with amazing accuracy. Mechanical testing has certainly come a long way since the time of Galileo, who used rocks to test the strength of cantilever wooden beams.
Today the most advanced testing setups rely on digital image correlation (DIC) with multiple cameras to measure strain on the surface of a specimen as it deforms under applied load. This allows us to identify regions of maximum strain, visualize crack initiation/propagation, and even compare directly with finite element models which solve the equations of elasticity. However, did you know that for years, engineers relied on a much simpler method for measuring strain during mechanical testing, that of applying brittle coatings to specimens?
The procedure for strain measurement with brittle coatings is as follows. Before testing, coat your specimen with a thin, brittle lacquer made of a clay-like material. After the coating has hardened, conduct the test as normal. During the test, look for the first crack to appear on the specimen. The location of this crack indicates the region of maximum strain, and the direction perpendicular to the crack corresponds to the direction of maximum tensile stress. Then, as more cracks develop on the surface, the coating forms isostatic lines which visualize the load path and indicate regions of constant stress. With calibration tests on bars coated with the brittle lacquer, the magnitude of the stress can be approximated as well. And for even larger deformations, flaking of the coating indicates potential regions of plasticity and compressive strains.
The simplicity and elegance of this method led to its widespread adoption starting in the 1930s. The key benefit of the technique was that it could be used to measure strain on complicated structures for which theoretical models did not suffice. For instance, it quickly found use for testing of engine components such as crankshafts, connecting rods, and pistons. Eventually it was used on all types of specimens, from plastics, glasses, rubbers, to even bones. Below are some images from such tests with brittle coatings.

Brittle coating cracks on a crane hook subject to bending (right), compared to similar cracks on a calibration bar (left). The side-by-side comparison of crack spacings is used to estimate the magnitude of stresses on the hook (Stern 1979).
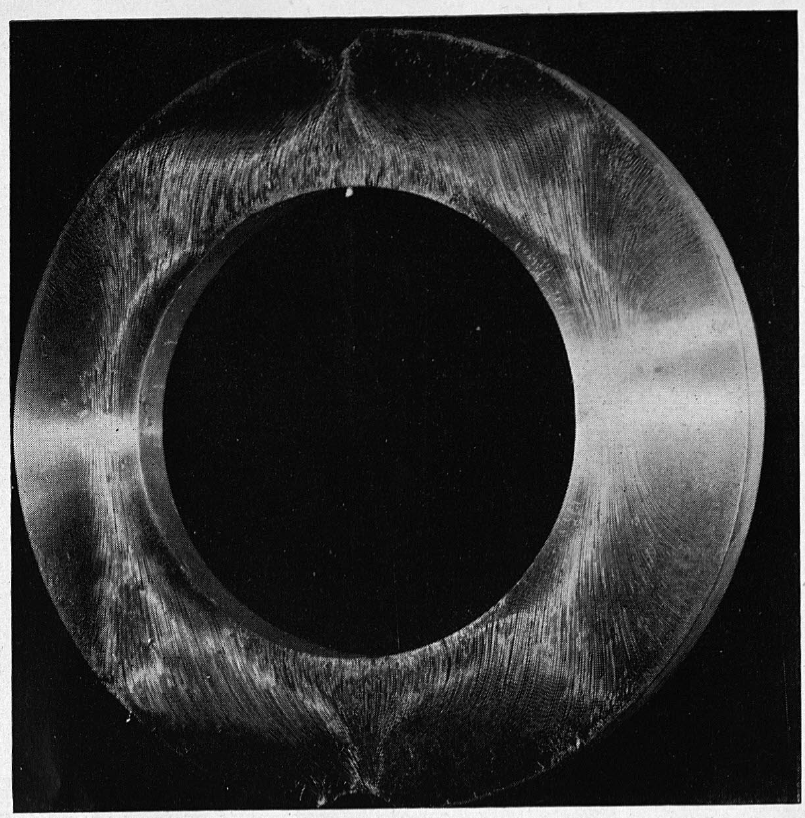

Brittle coating cracks on an aluminum ring subject to concentrated compressive forces at the top and bottom. The cracks on the surface indicate the load path and direction of tensile stresses. On the right, a comparison of the estimated stresses from the brittle coating technique with both photoelasticity and an analytical solution (Salmon 1950).
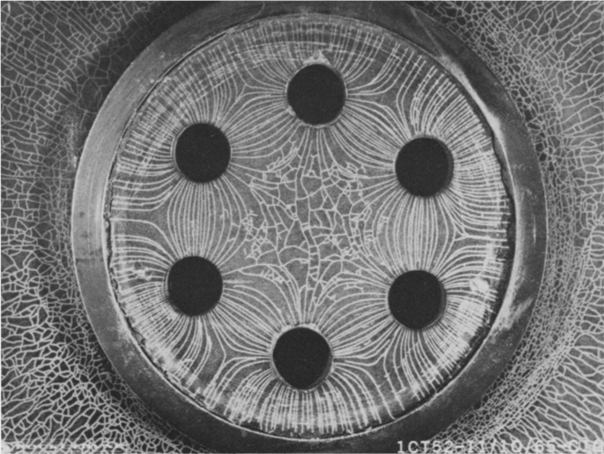
Brittle coating cracks on a turbine disk rotated at high speed. The tensile hoop stress from rotation causes radial cracks in the coating (Stern 1979).

Brittle coating cracks on a piston subject to hydraulic pressure (Salmon 1950).

Brittle coating cracks on a human jawbone (Stern 1979).
As these images show, the brittle coating approach found use for a variety of applications, from rotating turbine disks to human jawbones. Given the simplicity of the approach, it is remarkable that the coating cracks accurately predicted strains and stresses (as evidenced by the ring specimen). This measurement accuracy was not a coincidence, however. Between the 1930s and 1970s, researchers perfected the art of applying brittle coatings to measure strain. Numerous studies investigated the effect of thickness, drying time, temperature, and humidity on the accuracy of strain measurement, leading to optimum drying times and thickness specifications for certain coatings. For example, one of the most popular brittle coatings called StressCoat (developed at MIT by Greer Ellis) required a drying time of 15 to 24 hours, a uniform thickness of 0.004 in, and a temperature fluctuation of ±5° F during testing to achieve a strain sensitivity of 0.07%.
While the brittle coating technique was accurate and versatile, it did have caveats which eventually led to its decline. First, applying the coating with uniform thickness was no easy task and required hours of practice. Even having small bubbles in the coated layer affected the sensitivity of strain measurement (sometimes in a good way!). Second, the principle that the behavior of a coated specimen is the same as an uncoated specimen assumes perfect adhesion between the coating and substrate as well as a match in their constitutive properties. However, in reality the coated specimen may behave differently, as the coating may slightly stiffen the specimen surface and have different mechanical properties which affect the sensitivity of strain measurement. For example, although the coatings are generally brittle, they may creep at high temperatures before the specimen and give an inaccurate description of strain.
Ultimately the popularity of the brittle coating technique began to decline in the 1970s, as the finite element method (FEM) began its rise to fame. As people grew confident in FEM models, there was no need to go through the arduous process of testing complicated components with the brittle coating technique; coupon tests on simple geometries were enough to verify the material properties used in the models. In addition, electronic strain gauges placed on the specimen offered an easy way of precisely measuring strain on the surface. While the strain gauges could not immediately identify regions of maximum strain, they were easier to handle and just as precise as the best brittle lacquers. And when digital image correlation (DIC) techniques were invented which required only two cameras and a speckle pattern to measure three-dimensional strain, the time-consuming process of applying brittle coatings really began to lose popularity.
Today, the brittle coating technique is mainly a lost art used for testing only the most complicated components and some non-destructive evaluation. Strain gauges and DIC have taken over for almost all experimental stress analysis. Boeing, for instance, conducts its static and fatigue testing of airplanes with thousands of strain gauges, tens of cameras, and extremely precise load cells (I’ve seen it!). Nonetheless, strain measurement with brittle coatings has a certain simplicity and elegance that is worth remembering for our mechanical testing and engineering today.
Next week’s blog: photoelasticity!
References/further reading:
History of Strength of Materials, Timoshenko 1953.
“Brittle Coatings for Quantitative Strain Measurements,” A.V. de Forest, Greer Ellis, Ferdi B. Stern, 1942.
“The Measurement of Strain in Components of Complicated Form by Brittle Lacquer Coatings,” W.J. Clenshaw 1944.
“Stress Analysis with Brittle Lacquer: A Method for the Experimental Evaluation of Loads Developed in Components of Complex Shape,” B. Salmon 1950.
“Brittle Coatings,” Ferdi B. Stern 1979.
“Brittle Lacquer for Acoustic Testing of Structure,” Ronald F. Kocka 1977.
Comments